TOPICS
Mission
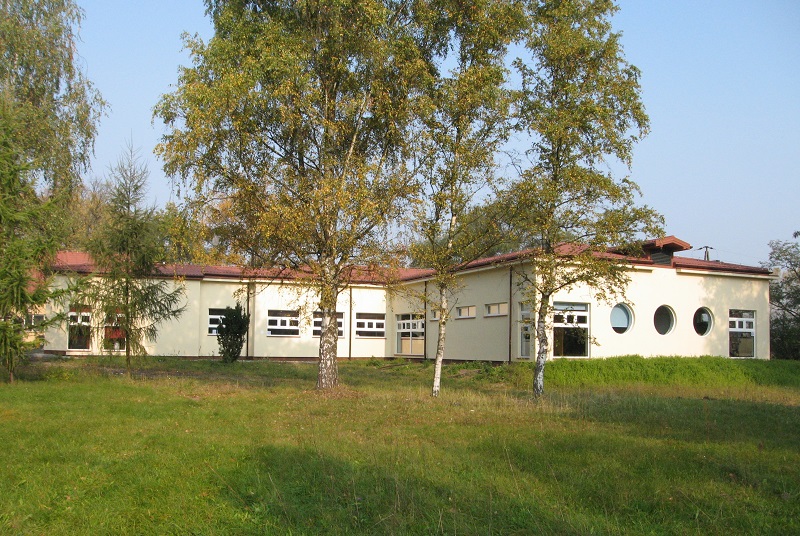
Laboratory of Plastic Deformation Under High Pressure, Institute of High Pressure Physics of the Polish Academy of Sciences, Celestynów
Institute of High Pressure Physics of the Polish Academy of Sciences UNIPRESS has for many years occupied leading positions in rankings of scientific institutions in Poland. Laboratory of Plastic Deformation Under High Pressure UNIPRESS is one of the most modern research and development institutions dealing with technologies of plastic processing of metals and their alloys with severe plastic deformation (SPD).
The laboratory offers a wide range of collaborations in the fields of physics, materials engineering and mechanics, in particular:
- Know-how of hydrostatic extrusion technology,
- Severe plastic deformation of metals and alloys,
- Plastic deformation of hard and brittle materials,
- Hydrostatic extrusion of thin wires,
- Consolidation and forming of powders and composites,
- Making small commercial series of products with complex shapes,
- Design of high-pressure equipment,
- Structural, surface and mechanical property analysis of materials.
History
It is the increasing demand for materials that are difficult to form that has become the main reason for the search and development of new methods of forming metals and alloys.
The use of high pressure for plastic deformation was stimulated by the fact that the ductility of metals increases as the surrounding hydrostatic pressure increases. An American scientist, Percy Williams Bridgman (1882-1961) did the most distinguished work in the field of high pressure at Harvard University in the USA, for which he was awarded the Nobel Prize in 1946. He was the first to pioneer experiments in hydrostatic extrusion, a plastic processing method first named as such in 1961 by Welshman Hubert Lloyd David Pugh (1914-2005) of the NEL National Laboratory in East Kilbride, Scotland. Hydrostatic extrusion involves extruding a charge through a die using a medium compressed to high pressure, as opposed to the conventional extrusion process where a piston pushes against the material. The pressurised medium coats the entire deformable charge, exerting hydrostatic pressure on both its sides and back. Work by Bridgman and later by Pugh confirmed an approximately linear increase in ductility of steel with pressure and a faster than linear increase for other materials. In some cases, such as for zinc at critical pressure, a rapid brittle-plastic transformation is observed. Nevertheless, the main conclusion from this precursor work is that the ductility of all the metals studied increases with increasing hydrostatic pressure.
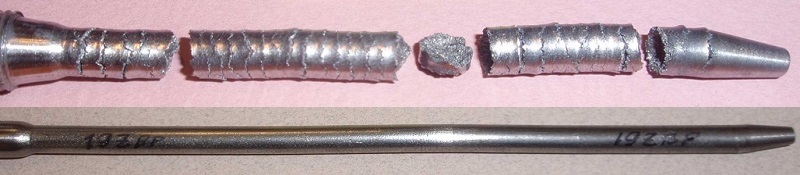
– High pressure inhibits cracking which allows plastic deformation of brittle materials; Normally brittle grey cast iron: (top) after extrusion to atmospheric pressure, (bottom) to 4,000 atmospheres.
Polish roots
Work on hydrostatic extrusion technology was initiated in Poland by Wacek Pachla and Ludwik Styczyński of the UNIPRESS Institute of High Pressures Physics of the Polish Academy of Sciences in 1973. They intensively studied the process of hydrostatic extrusion from the theoretical point of view and carried out significant experimental work examining the relation between the extrusion pressure and the strain rate for a wide range of engineering construction materials and the resulting properties of the extruded products. They focused particular attention on the mechanical properties of extruded products and explaining the reasons for the higher strength compared to products deformed by traditional methods such as drawing, conventional extrusion, rolling or forging. Quickly, work involving the transformation of materials by hydrostatic extrusion transformed its character from pure academic curiosity to the study of a process with considerable application potential.
Beginnings
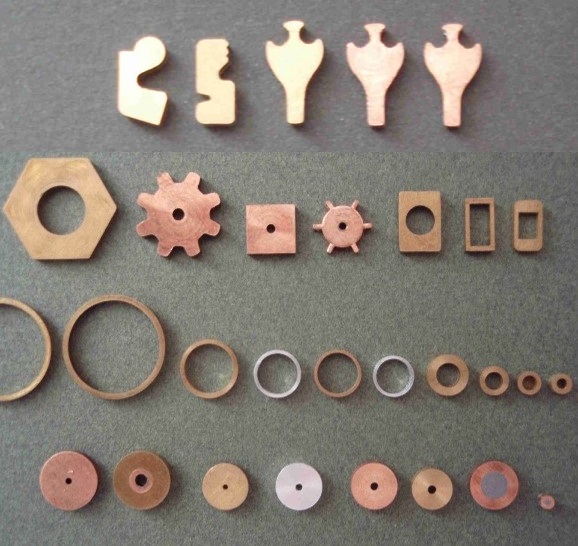
The UNIPRESS hydrostatic extrusion technology enables the manufacture of profile products with complex external and internal cross-sections
From the very beginning, work on hydrostatic extrusion at UNIPRESS focused on the application aspects of this technology and its commercialisation. The first practical results included the production of ultra-thin bonding wires for electronics (1986-1994), multi-core solder wires (since 1984 produced by the first so-called spin off company Cynel Unipress), bimetal wires (since 1984 produced by the first so-called spin off company Cynel Unipress). The production of ultra-thin contact wires (bonding wires) for electronics (1986-1994), multi-core soldering wires (from 1984 produced by the first so-called spin-off company Cynel Unipress), bi-metal copper-lead rods for the regeneration of bearings (1988-1989), thick-walled capillary tubes from alloyed copper for welding apparatus tips (from 1989, in the years 1993-1997 produced in STPoland, in which UNIPRESS was a shareholder) or prototype thin-walled aluminium tubes for the automotive industry (1989). Research work in the field of extrusion technology was accompanied by the development of original presses and auxiliary equipment for hot and cold hydrostatic extrusion technology. In 1986, a new 400 ton hydrostatic extrusion press operating up to 1000oC was put into service, which created new technological possibilities. Technologies of extrusion of thin-walled copper tubes (1989-1990) and brass tubes and profiles (1994) were developed and practically applied. In parallel, work was carried out on the hydrostatic extrusion of other materials, such as metals for electrical contacts, noble metals or metals based on intermetallic compounds. The experience and know-how gained in the field of hydrostatic extrusion technology enabled the founding of a second spin-off company, Hydron Unipress (1988), which, among other things, specialised in the construction of presses, including those for hydrostatic extrusion.
Breakthrough
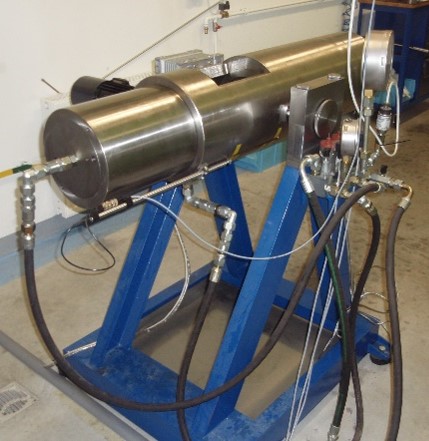
UNIPRESS has a set of modern hydrostatic extrusion machines enabling the production of ultra-high-strength materials at pressures up to 25,000 atmospheres
A significant breakthrough in the practical applicability of hydrostatic extrusion came when, for the first time in the world, UNIPRESS began to apply this method to various metals and alloys as a ‘severe plastic deformation’ method (SPD) method. This became possible thanks to the development of the method of cumulative hydrostatic extrusion, in which the total large plastic deformation is realised by multiple repeated extrusion processes with smaller deformations. Since then (early 2000), the prospects for industrial applications of extrusion have exploded. Why? Because large plastic deformation using hydrostatic extrusion enables significant fragmentation of microstructure in metals and alloys, which in consequence leads to significant increase in their strength, hardness, resistance to brittle fracture, fatigue strength and superplasticity (creep).
Nanomaterials
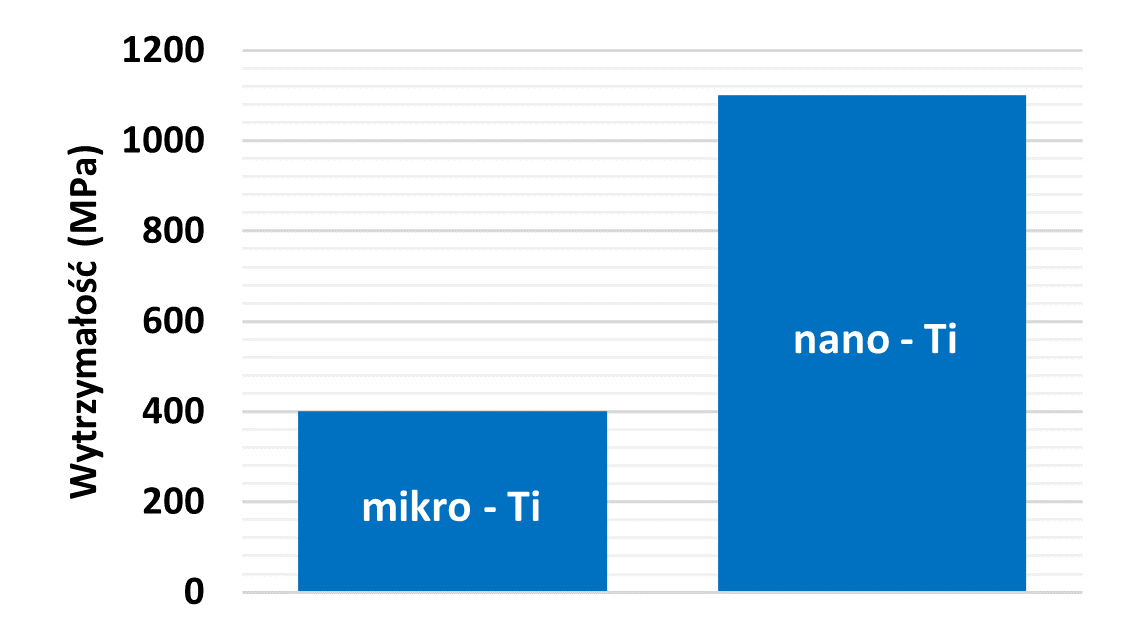
Severe plastic deformation induced by hydrostatic extrusion allows for a significant refinement of the microstructure in metals and alloys, which results in a significant increase in their strength
Industrial potential
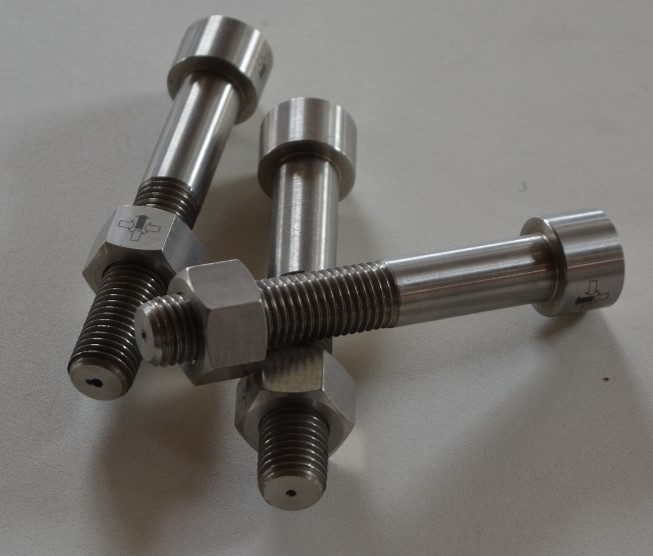
The world’s strongest offered bolts made of acid-resistant austenitic steel A4 according to ISO, manufactured from cold-hardened material by hydrostatic extrusion; the bolts’ durability in a sea atmosphere is 100 years