TEMATYKA
Misja
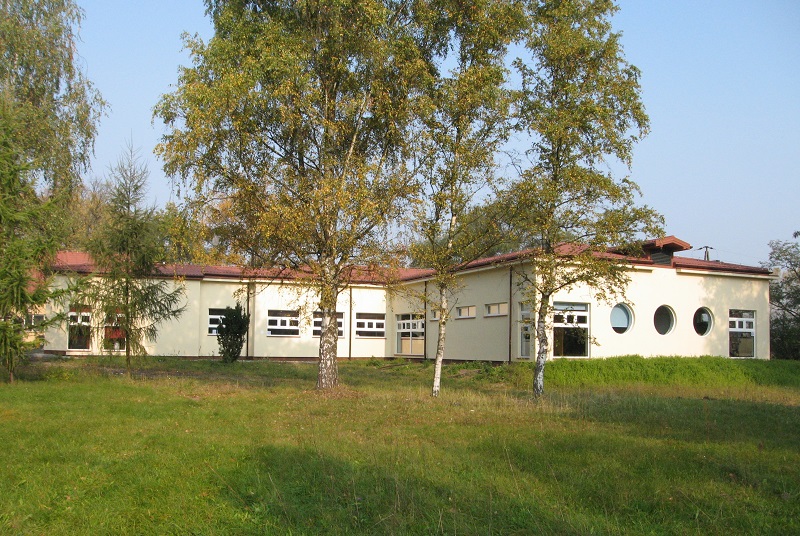
Laboratorium Plastyczności pod Wysokim Ciśnieniem, Instytut Wysokich Ciśnień Polskiej Akademii Nauk UNIPRESS, Celestynów
Instytut Wysokich Ciśnień Polskiej Akademii Nauk UNIPRESS od lat zajmuje czołowe miejsca w rankingach placówek naukowych w Polsce. Laboratorium Plastyczności pod Wysokim Ciśnieniem UNIPRESS jest jedną z najnowocześniejszych placówek badawczo-rozwojowych, zajmującą się technologiami przeróbki plastycznej metali i ich stopów z dużymi odkształceniami plastycznymi (SPD, ang. severe plastic deformation).
Laboratorium oferuje szeroki zakres współpracy w dziedzinie fizyki, inżynierii materiałowej i mechaniki, a w szczególności:
- Know-how technologii wyciskania hydrostatycznego,
- Duże odkształcenia plastyczne metali i stopów,
- Odkształcanie plastyczne materiałów twardych i kruchych,
- Wyciskanie hydrostatyczne cienkich drutów,
- Konsolidacje i formowanie proszków i kompozytów,
- Wykonywanie niewielkich serii handlowych produktów o złożonych kształtach,
- Projektowanie urządzeń wysokociśnieniowych,
- Analizę strukturalną, powierzchni i własności mechanicznych materiałów.
Historia
To właśnie wzrastające zapotrzebowanie na trudne do odkształcania plastycznego materiały stało się w głównym powodem do poszukiwań i rozwoju nowych metod obróbki plastycznej metali i stopów.
Zastosowanie wysokiego ciśnienia do przeróbki plastycznej było stymulowane poprzez fakt, że plastyczność metali wzrasta wraz ze wzrostem otaczającego je ciśnienia hydrostatycznego. Amerykański naukowiec, Percy Williams Bridgman (1882-1961) wykonał najbardziej wyróżniające się prace w dziedzinie wysokich ciśnień na Uniwersytecie Harwarda w USA, za które został nagrodzony nagrodą Nobla w 1946 roku. Był pierwszym, który zapoczątkował eksperymenty w dziedzinie wyciskania hydrostatycznego, metody przeróbki plastycznej nazwanej tak po raz pierwszy w 1961 roku przez Walijczyka Huberta Lloyda Davida Pugh (1914-2005) z Narodowego Laboratorium NEL w East Kilbride w Szkocji. Wyciskanie hydrostatyczne polega na wyciskaniu wsadu przez matrycę przy pomocy sprężonego do wysokiego ciśnienia medium w odróżnieniu od konwencjonalnego procesu wyciskania, w którym tłok naciska na materiał. Medium ciśnieniowe oblewa cały odkształcany wsad, wywierając ciśnienie hydrostatyczne zarówno na jego boki jak i tył. Prace Bridgmana i późniejsze Pugh potwierdziły w przybliżeniu liniowy wzrost plastyczności stali wraz z ciśnieniem i szybszy niż liniowy wzrost dla innych materiałów. W niektórych przypadkach, jak np. dla cynku w krytycznym ciśnieniu obserwuje się gwałtowną przemianę kruchy-plastyczny. Niemniej jednak, głównym wnioskiem wynikającym z tych prekursorskich prac jest, że plastyczność wszystkich badanych metali wzrasta wraz ze wzrostem ciśnienia hydrostatycznego.
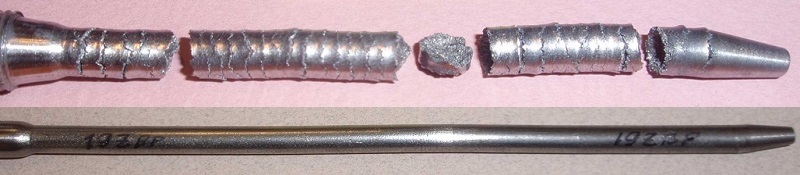
Wysokie ciśnienie powstrzymuje pękanie co umożliwia odkształcanie plastyczne materiałów kruchych; Normalnie kruche żeliwo szare: (góra) po wyciskaniu do ciśnienia atmosferycznego, (dół) do ciśnienia 4 000 atmosfer
Polskie korzenie
Prace nad technologią wyciskania hydrostatycznego zostały zapoczątkowane w Polsce przez Wacka Pachlę i Ludwika Styczyńskiego z Instytutu Wysokich Ciśnień Polskiej Akademii Nauk UNIPRESS w 1973 roku. Badali oni intensywnie proces wyciskania hydrostatycznego pod kątem teoretycznym jak i przeprowadzili istotne prace doświadczalne badając zależność pomiędzy ciśnieniem wyciskania a stopniem odkształcenia dla szerokiego zakresu inżynierskich materiałów konstrukcyjnych oraz wynikających z nich własności wyciśniętych produktów. Szczególną uwagę poświęcili własnościom mechanicznym wyciskanych produktów i wyjaśnieniu przyczyn wyższej wytrzymałości w porównaniu z produktami odkształcanymi tradycyjnymi metodami jak ciągnienie, wyciskanie konwencjonalne, walcowanie czy kucie. Szybko, prace obejmujące transformację materiałów na drodze wyciskania hydrostatycznego przekształciły swój charakter z czystej, akademickiej ciekawości do badań procesu o znacznym potencjale aplikacyjnym.
Początki
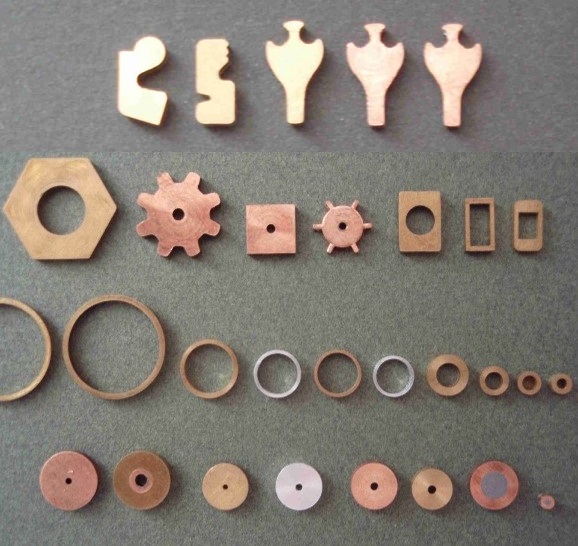
Technologia wyciskania hydrostatycznego UNIPRESSu pozwala wytwarzać produkty profilowe o złożonych przekrojach zewnętrznych i wewnętrznych
Od samego początku prace nad wyciskaniem hydrostatycznym w UNIPRESS-ie koncentrowały się na aplikacyjnych aspektach tej technologii i jej komercjalizacji. Pierwsze praktyczne wyniki obejmowały wytwarzanie ultra-cienkich drutów kontaktowych (bonding wires) dla elektroniki (1986-1994), wielordzeniowych drutów lutowniczych (od 1984 produkowanych przez pierwszą tzw. firmę spin off Cynel Unipress), bimetalowe pręty miedziano-ołowiane do regeneracji panewek (1988-1989), grubościenne rurki kapilarne z miedzi stopowej na końcówki aparatów spawalniczych (od 1989, w latach 1993-1997 produkowane w firmie STPoland, której udziałowcem był UNIPRESS) czy też prototypowe cienkościenne rurki aluminiowe dla przemysłu samochodowego (1989).
Pracom badawczym w dziedzinie technologii wyciskania towarzyszył rozwój oryginalnych pras i wyposażenia pomocniczego dla technologii wyciskania hydrostatycznego na zimno i na gorąco. W 1986 roku uruchomiono nową 400 tonową prasę do wyciskania hydrostatycznego pracującą do 1000oC co stworzyło nowe możliwości technologiczne. Zostały opracowane i praktycznie zastosowane technologie wyciskania cienkościennych rurek miedzianych (1989-1990) oraz rurek i profili mosiężnych (1994). Równolegle, prowadzone były prace nad wyciskaniem hydrostatycznym innych materiałów, jak metali na styki elektryczne, metali szlachetnych czy metali na bazie związków intermetalicznych. Zdobyte doświadczenie ‘know-how’ w dziedzinie technologii wyciskania hydrostatycznego pozwoliły na założenie drugiej firmy spin-off Hydron Unipress (1988), która m.in. specjalizuje się w budowie pras, w tym do wyciskania hydrostatycznego.
Przełom
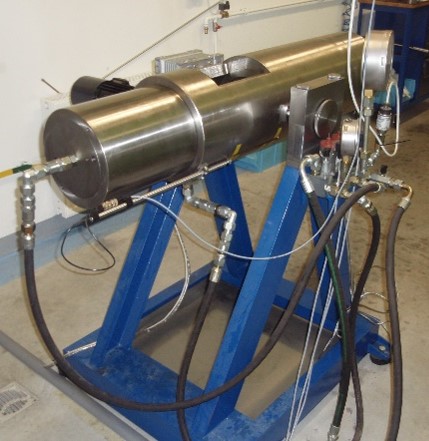
UNIPRESS posiada komplet nowoczesnych pras do wyciskania hydrostatycznego umożliwiający wytwarzanie ultra-wytrzymałych materiałów w ciśnieniach do 25 000 atmosfer
Autentyczny przełom w możliwościach praktycznego stosowaniu wyciskania hydrostatycznego nastąpił, kiedy po raz pierwszy na świecie w UNIPRESSie zaczęto stosować tę metodę do różnych metali i stopów jako metodę ‘dużych odkształceń plastycznych’ (ang. severe plastic deformation SPD). Stało się to możliwe dzięki opracowaniu metody kumulacyjnego wyciskania hydrostatycznego, w którym całkowite duże odkształcenie plastyczne realizowane jest na drodze wielokrotnie powtarzanych procesów wyciskania z mniejszymi odkształceniami. Od tego momentu (początki 2000) perspektywy przemysłowych zastosowań procesu wyciskania wręcz eksplodowały. Dlaczego ? Ponieważ duże odkształcenia plastyczne przy zastosowaniu wyciskania hydrostatycznego umożliwiają znaczne rozdrobnienie mikrostruktury w metalach i stopach co w konsekwencji prowadzi do znacznego wzrostu ich wytrzymałości, twardości, odporności na kruche pękanie, wytrzymałości zmęczeniowej i nadplastyczności (pełzania).
Nanomateriały
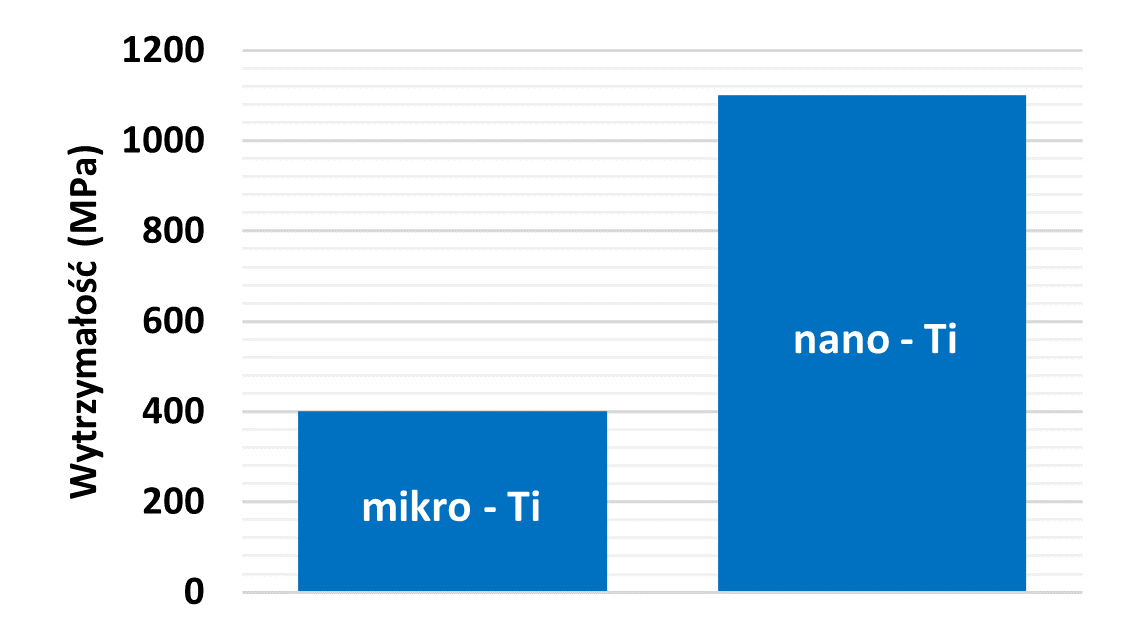
Duże odkształcenia plastyczne wywołane metodą wyciskania hydrostatycznego umożliwiają na znaczne rozdrobnienie mikrostruktury w metalach i stopach co w konsekwencji prowadzi do znacznego wzrostu ich wytrzymałości
Od kiedy kumulacyjne wyciskanie hydrostatyczne prowadzące do dużych odkształceń plastycznych zastało zastosowane praktycznie w UNIPRESSie wytwarzanie metali i stopów o strukturze nanokrystalicznej (nanometali) o wielkości ziaren poniżej 100nm stało się standardem. Potwierdzono to dla handlowo czystego tytanu (47nm), czystego żelaza i brązu krzemowego (60nm), duraluminium (65nm), stali Eurofer 97 (86nm) czy też stali austenitycznej i czystego niklu (100nm). Inne badane materiały plasowały się w zakresie ultradrobnoziarnistym, jak miedź (120nm), stop miedzi z chromem i cyrkonem (140nm), związek intermetaliczny niklu z aluminium (300nm) czy stop tytanu z aluminium i wanadem (200-400nm). Skala rozdrobnienia mikrostruktury staje się łatwiejsza do zrozumienia jeśli porówna się ją ze średnią grubością ludzkiego włosa wynoszącą 50 000nm. Oznacza to, iż ok. 1 000 ziaren tytanu lub 500 ziaren stali austenitycznej zmieści się na przekroju poprzecznym włosa. Tak drastyczne rozdrobnienie mikrostruktury prowadzi do własności wytrzymałościowych wyciskanych hydrostatycznie metali nieosiągalnych dla ich konwencjonalnych, wytwarzanych metodą tradycyjną odpowiedników.
Potencjał przemysłowy
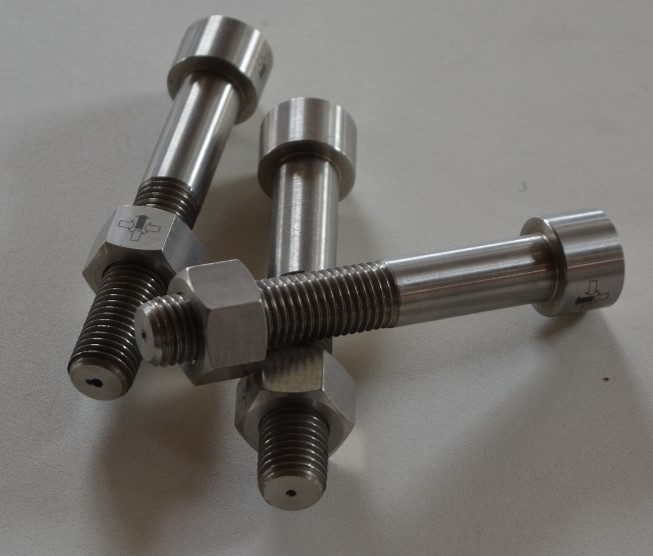
Najmocniejsze oferowane na świecie śruby z kwasoodpornej stali austenitycznej A4 wg ISO wytworzone z utwardzonego na zimno materiału metodą wyciskania hydrostatycznego; trwałość śrub w atmosferze morskiej 100 lat
Rozwój nowoczesnych gałęzi przemysłu wymaga ‘nowych’ materiałów spełniających ostre warunki konstrukcyjne związane z wytrzymałością, temperaturą pracy czy twardością. Duże odkształcenia plastyczne pozwalają często nadać materiałom unikalne własności świadczące o wytworzeniu ‘nowego’ materiału. Tak jest w przypadku wyprodukowania metodą wyciskania hydrostatycznego metali lekkich jak stopy magnezu czy duraluminium o wytrzymałościach na zrywanie przekraczając odpowiednio 400MPa i 600MPa. Świadczy o tym również wytworzenie metodą wyciskania hydrostatycznego wolnego od szkodliwych dla człowieka składników stopowych czystego tytanu (99.99+%), o wytrzymałości powyżej 1300MPa, o ¼ przekraczającej wytrzymałość używanego dotychczas na implanty stopu tytanu z aluminium i wanadem. Trzy wymienione wyżej metale należą do najlżejszych, powszechnie stosowanych materiałów konstrukcyjnych, o najwyższych proporcjach wytrzymałości do wagi. Stąd ich ogromne znaczenie w takich obszarach jak transport czy implanty medyczne. Innym materiałem o istotnym znaczeniu konstrukcyjnym jest kwasoodporna stal austenityczna. Jej wytrzymałość została na drodze umocnienia na zimno poprzez wyciskanie hydrostatyczne podniesiona do zakresu (800-1200MPa) nieosiągalnego dla jej mikrokrystalicznych odpowiedników o podobnym składzie stopowym. Śruby wykonane z tej stali pracują już za granicą. Przetworzone metodą wysokociśnieniową czysty tytan i stal austenityczna są bezpośrednimi kandydatami do zastosowań przemysłowych. Wiele innych materiałów konstrukcyjnych przetworzonych w UNIPRESSie metodą wyciskania hydrostatycznego może również wyprzeć materiały tradycyjne. Stal Eurofer 97 jako materiał na części aparatury do syntezy jądrowej, czysty nikiel 99.98% na układy mikro-elektro-mechaniczne (MEMS) czy też stopy aluminium serii 5XXX, 6XXX i 7XXX na wysokowytrzymałe nity konstrukcyjne i części maszyn są tego arbitralnymi przykładami.