Tango IV
Innowacyjne elektrody do procesu drążenia elektroerozyjnego o podwyższonej żywotności
Celem projektu jest opracowanie nowej generacji elektrod do procesu drążenia elektroerozyjnego wgłębnego (EDM) w oparciu o wyniki badań zrealizowanego projektu bazowego. Realizacja projektu będzie polegała na optymalizacji procesu wysokociśnieniowej przeróbki plastycznej metodą wyciskania hydrostatycznego (HE) miedzi 99.95% oraz miedzi stopowej CuCrZr mającej na celu uzyskanie materiałów o ultradronoziarnistej mikrostrukturze charakteryzujących się zmniejszoną podatnością na zużycie elektroerozyjne zachodzące w procesie drążenia elektroerozyjnego wgłębnego. Realizacja tego celu będzie możliwa dzięki zastosowaniu niekonwencjonalnej metody wysokociśnieniowej przeróbki plastycznej w postaci procesu wyciskania hydrostatycznego, która charakteryzuje się wytwarzaniem materiałów o wyraźnej anizotropii strukturalnej w postaci morfologii wydłużonych ziaren w kierunku osi wyciskania.
Przesłankami, stanowiącymi podstawę do podjęcia badań w przedstawionym projekcie stały się wyniki badań autorów zrealizowane i opisane w ramach projektu bazowego pt. „Wpływ anizotropii mikrostruktury materiałów wyciskanych hydrostatycznie na ich właściwości termo-fizyczne”, (Preludium 9, nr: 2015/17/N/ST8/01471). W ramach badań zaobserwowano wyraźny wpływ rozdrobnienia mikrostruktury, jak również jej morfologii, na zmianę właściwości deformowanych materiałów, w tym właściwości termofizycznych takich jak dyfuzyjność cieplna (a), przewodność cieplna (λ) i ciepło właściwe (cp). Na skutek zastosowanej wysokociśnieniowej przeróbki plastycznej metodą HE uzyskano w badanych materiałach ultradrobnoziarniste mikrostruktury charakteryzujące się bardzo dużą liczbą skumulowanych defektów powierzchniowych, liniowych i punktowych mających istotny wpływ na ograniczenie wymiany ciepła, a tym samym zmianę badanych właściwości termofizycznych. Zmiany te sięgały nawet kilkunastu procent w przypadku analizy przekrojów poprzecznych i kilku procent w przypadku analizy przekrojów wzdłużnych. Potwierdziło to wpływ anizotropii i charakterystycznej dla procesu HE morfologii struktury na zmianę właściwości termofizycznych.
Wszystkie te przesłanki pozwoliły na podjęcie badań wstępnych, dotyczących zużycia materiałów po procesie HE, w warunkach drążenia elektroerozyjnego wgłębnego. Autorzy wykonali próby drążenia stali 45HNMF elektrodą wykonaną z miedzi 99,95% w postaci walca o średnicy 20mm. Przedmiotem analizy było zużycie elektrody, jak również jakość powierzchni elementu drążonego (powierzchni obrabianej). Oba wyniki były zweryfikowane i odniesione do analogicznych badań realizowanych w oparciu o elektrodę wykonaną z miedzi 99,95% w stanie nieodkształconym. W obu badanych parametrach zaobserwowano wyraźny efekt zastosowania materiału po procesie HE. Uzyskano zmniejszenie zużycia o około 20%, (Rys. 1) przy jednoczesnej poprawie jakości powierzchni obrabianej, dla której chropowatość zmniejszyła się nawet o 30%, (Rys. 2).
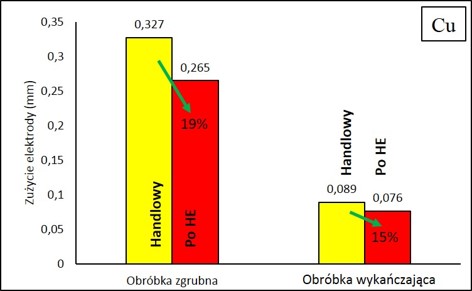
Rys. 1. Zużycie elektrody z miedzi 99,95% po procesie HE.
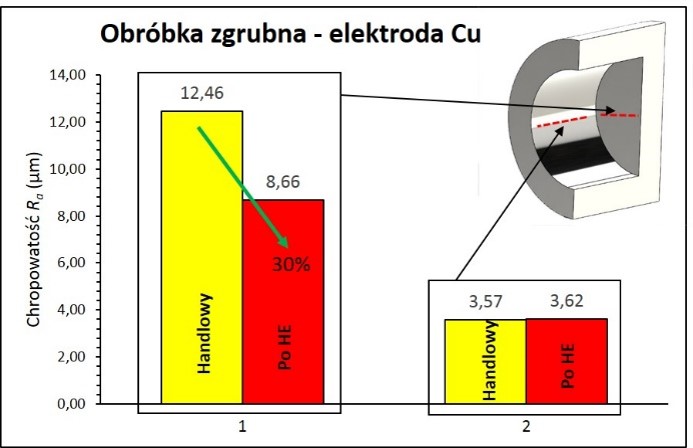
Rys. 2. Chropowatość powierzchni w obróbce zgrubnej przy wykorzystaniu elektrody z miedzi po procesie HE.
Otrzymane produkty w postaci elektrod EDM charakteryzować się będą zwiększoną żywotnością uzyskaną poprzez przyjazną środowisku obróbkę plastyczną na zimno, połączoną z klasyczną obróbką skrawaniem. Kontrolowanie ścieżki odkształcenia plastycznego, głównie wielkości i szybkości odkształcenia oraz chłodzenia produktu, umożliwi świadome kontrolowanie własności wyrobu w ich szerokim zakresie, a wytwarzane produkty będą charakteryzowały się funkcjonalnością użytkową przekładającą się na poprawę jakości powierzchni obrabianej zmniejszając tym samym koszty związane obróbką wykańczającą obrabianych form wtryskowych.
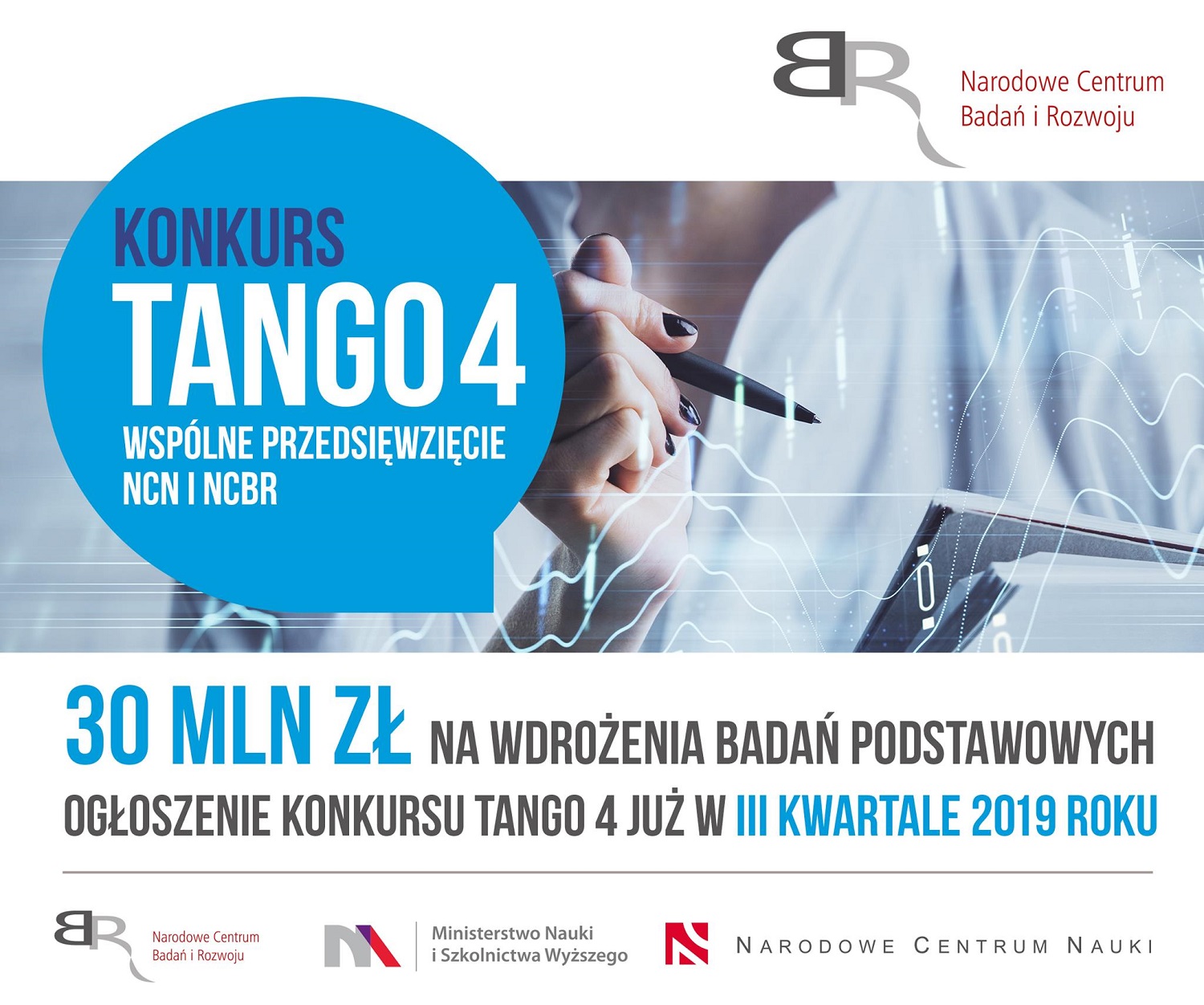