Lider XI
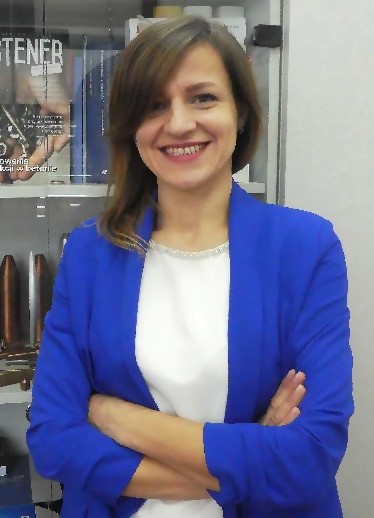
Highly deformable titanium for implantology applications
Dr Sylwia Przybysz, Eng. since January 2021 leads the project “Isotropic titanium for biomedical applications after large plastic deformation processes”, which received funding from the National Centre for Research and Development in the competition “Leader XI”.
The innovative method of plastic deformation of pure titanium will be based on a combination of two methods: the process of hydrostatic extrusion HE (Hydrostatic Extrusion) and the process of squeezing through an equiaxial angular channel ECAP (Equal Channel Anqular Pressing), the scheme of conducting such a process Fig. 1. Material deformed in this way will have a fragmented, isotropic structure and will be able to be used for medical implants, including for stabilization of bone fractures.
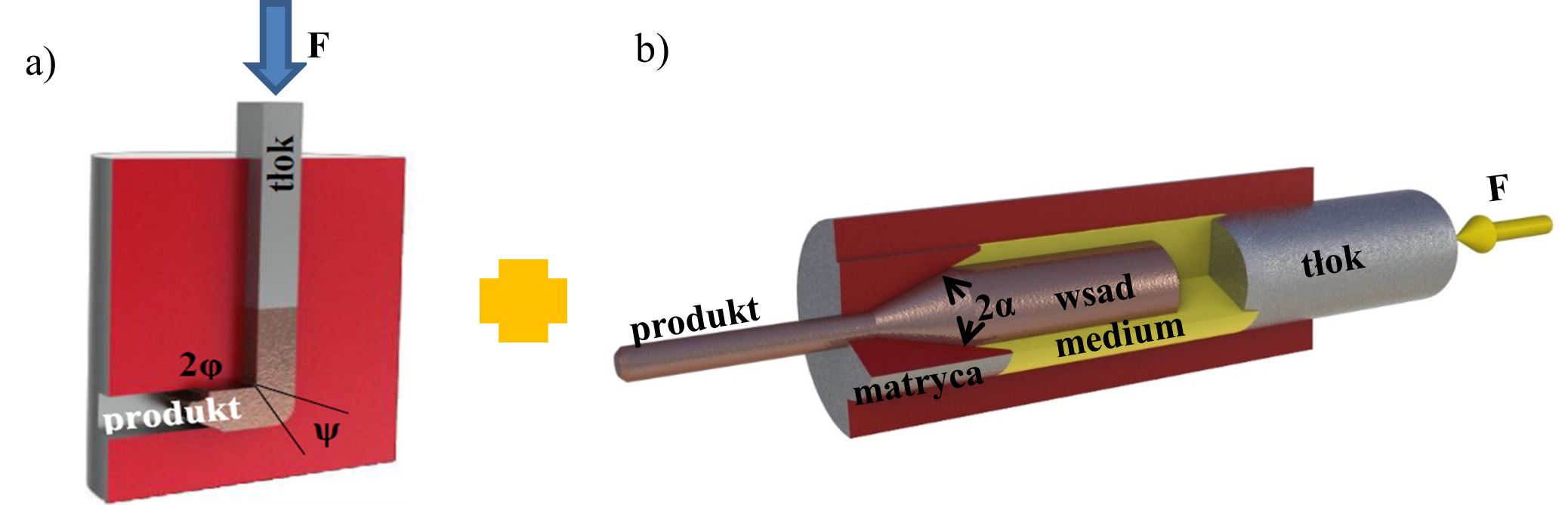
Figure 1: Schematic of the large plastic deformation method for obtaining nanocrystalline, isotropic and high-strength titanium, (a) ECAP, (b) HE
The fabrication of a nanostructure in pure titanium makes it possible to obtain a material with strength properties at the level of titanium alloy, while retaining the advantages of pure titanium. Nanotitanium is therefore an extremely attractive material for use in the manufacture of highly stressed implants.
The characteristic feature of the HE process is the generation of the so-called fibrous structure characterized by elongated grains in the direction of the axis of the extruded bar. This results in anisotropy of mechanical properties of the material after the deformation process in mutually perpendicular directions, Fig.2.
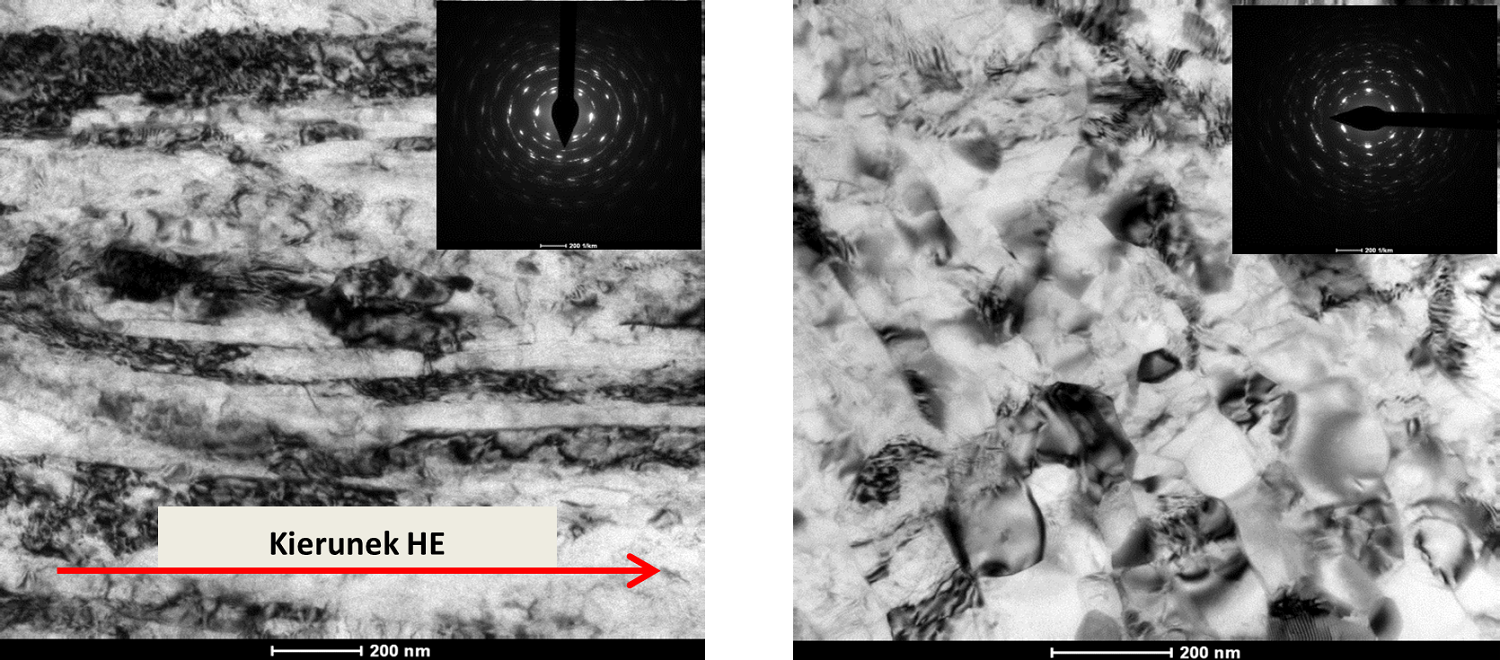
Fig.2 Anisotropic microstructure formed by hydrostatic extrusion process, a) longitudinal section and b) cross-section
Thanks to the technology applied in the project, the developed material for medical devices will be distinguished by its high mechanical strength, isotropic structure, biocompatibility and lack of harmful alloying elements such as aluminum, vanadium or niobium. The increased strength of the material, obtained through a complex plastic processing, will allow to reduce e.g. the diameter of screws used in implantology, and thus contribute to the reduction of the diameter of holes drilled in the bone, which are necessary for fixing implants.